3D Printing of Active Metals
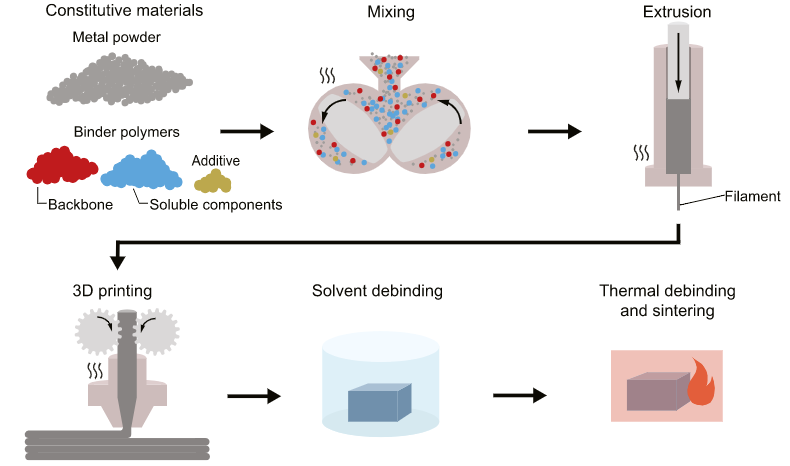
Filament-based material extrusion of metals (mMEX) is an additive manufacturing technique (AM) in which polymeric filaments loaded with metallic powder are extruded through a heated nozzle. As depicted in the schematic figure, first the constitutive materials are mixed to produce a homogeneous and printable filament. After printing, the post-processing includes a two-step debinding (solvent and thermal) and sintering. Given mMEX is a solid-state processing method, it is particularly advantageous for AM of materials containing volatile elements and results in more isotropic microstructures. mMEX offers enormous freedom to locally control material geometry and chemistry, allowing to reduce cost and waste, and to employ a large range of materials.
Currently we are working in the following aspects:
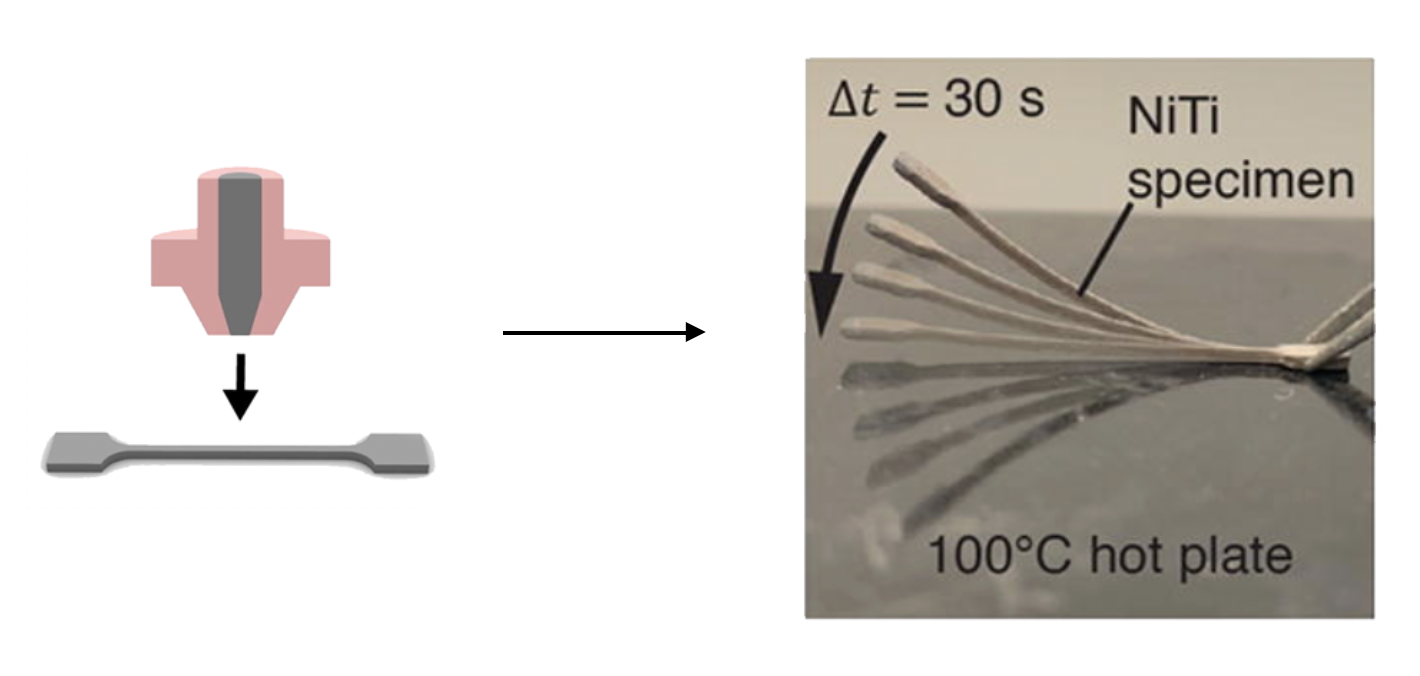
One of the research branches from additive manufacturing that has attracted interest in the last decade is printing of active materials (or 4D printing). Time is introduced as an additional parameter through materials that react to stimuli by changing their shape, properties or functionality.
Shape memory alloys (SMA) are metallic materials capable of recovering from strains past the elastic limit. Unlike conventional metals, they depend on solid-solid diffusionless phase transformations to return to the initial state. Consequently, they can also accommodate extraordinarily large deformations without showing brittle behavior. Analogous to thermally activated shape memory alloys, magnetic shape memory alloys (MSMAs) also show large recoverable deformation upon the application of a magnetic field.
Associated Publications:
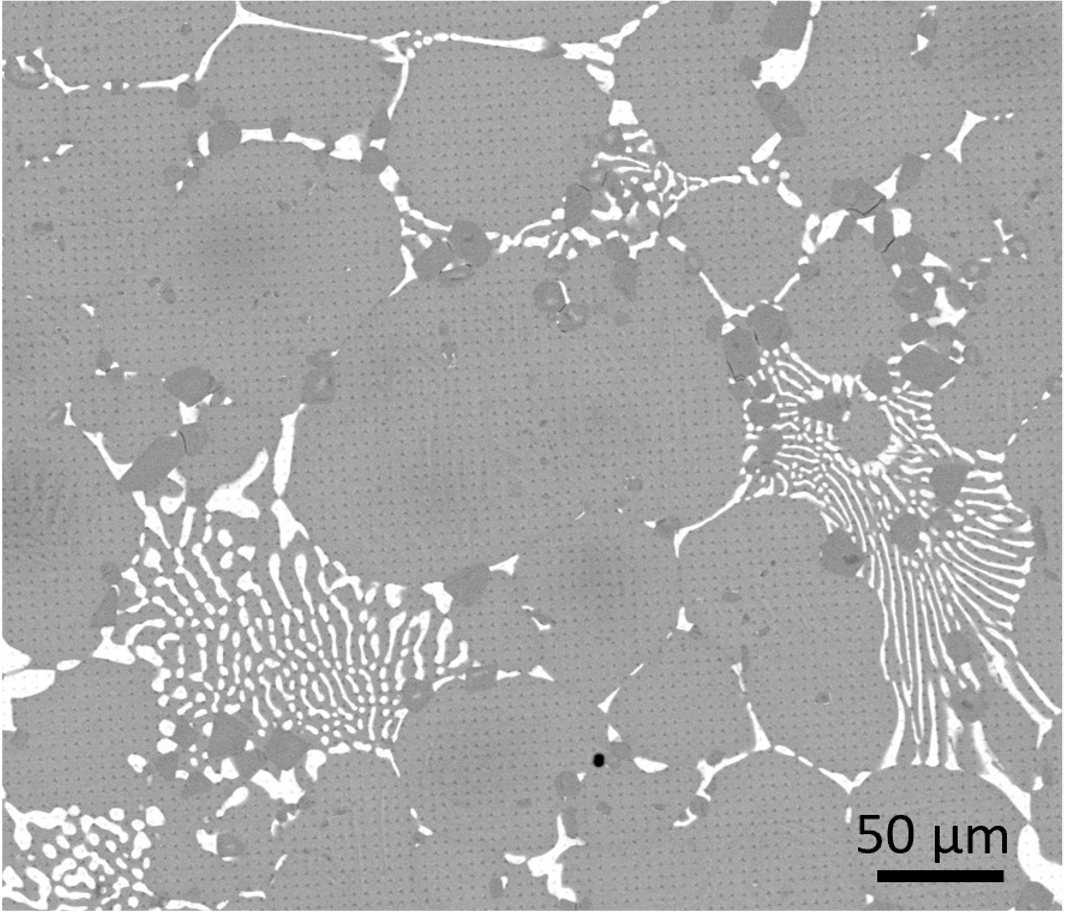
Due to the unique characteristics of this technique, material extrusion AM is particularly suitable for multi-material printing. Here, we explore the different combination of materials (active-structural or active-active) and the effect the printing process has on the result.
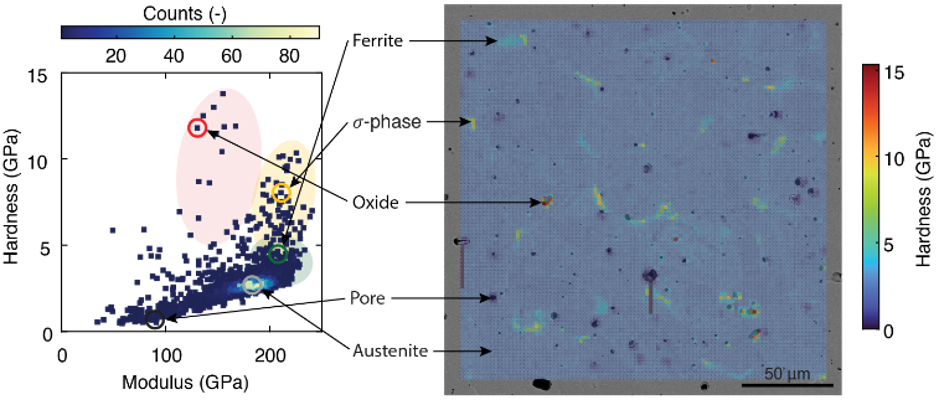
The mechanical characterization of materials in various length scales is necessary after producing our samples. From macro-scale testing down to micromechanics, we work on studying the behavior and microstructure of the materials we work with. SEM micrographs overlaid with indentation mappings enable the clear visualization of mechanical properties over a surface area (a sintered 316L specimen in this case). This technique is crucial in multi-metal parts as different phases are revealed and can be correlated to data clusters in 2D histograms.
Student Projects
If you are interested in any of these topics for your thesis or semester project, check out our protected page Student Projects. In case you are not enrolled at ETHZ, please contact .